فولاد ضد زنگ یا همان آهن زنگ نزن، یکی از مواد مهم در صنعت و ساخت و ساز است که به دلیل خواص خاص خود در برابر زنگ زدگی و خوردگی، در انواع مختلف مصارف مورد استفاده قرار میگیرد. در این مقاله، به بررسی گونههای مختلف فولاد ضد زنگ و کاربردهای آن میپردازیم. با ما همراه باشید تا در این سفر به دنیای فولاد ضد زنگ، هر آنچه را که باید بدانید، کشف کنیم.
فولاد ضد زنگ چیست؟
فولاد ضد زنگ یک نوع فولاد است که به دلیل ترکیبات شیمیایی خاص خود، مقاومت بالا در برابر زنگ زدگی و خوردگی را ارائه میدهد. اصطلاح “ضد زنگ” به اشاره به توانایی این نوع فولاد برای مقاومت در مقابل تاثیرات زنگ زدگی، خوردگی و تغییرات شیمیایی از جمله اکسیداسیون (اکسیژنگیری) میباشد.
فولاد ضد زنگ اغلب با افزودن عناصر آلیاژی مانند کروم، نیکل، مولیبدن و وانادیوم به فولاد معمولی تولید میشود. این عناصر باعث تشکیل یک لایه نازک و پایدار از اکسید بر روی سطح فولاد میشوند که از تماس مستقیم با مواد خارجی و اکسیژن هوا جلوگیری میکند. این لایه پاسیو (پایدار) باعث حفظ خواص مکانیکی و ظاهری فولاد میشود.
مقاومت فولاد ضد زنگ به زنگ زدگی و خوردگی آن تا حد زیادی به ترکیب شیمیایی و ساختار داخلی آن بستگی دارد. این انواع فولاد در انواع مختلف صنایع مانند صنایع خودروسازی، ساخت و ساز، صنایع شیمیایی، آشپزخانهها و بسیاری از مصارف دیگر استفاده میشوند.
تاریخچه و تکامل
تاریخچه و تکامل فولاد ضد زنگ از زمانی که اولین تلاشها برای تولید آن آغاز شد، یک داستان جذاب و پیچیده دارد. این نوع فولاد از اهمیت ویژهای در صنایع مختلف برخوردار شده است و تاکنون توسعهها و نوآوریهای متعددی در زمینه ترکیبات شیمیایی، فرآیندهای تولید و کاربردهای آن انجام شده است.
تاریخچه فولاد ضد زنگ به دهه 1910 میلادی بازمیگردد، زمانی که استیلیت (یک نوع فولاد ضد زنگ) برای اولین بار تولید شد. در ادامه دهههای 1920 و 1930، تحقیقات و آزمایشهای بیشتری برروی ترکیبات مختلف برای بهبود ویژگیهای فولاد ضد زنگ انجام شد.
اولین فولاد ضد زنگ به صورت آلیاژ، مارتنزیتی Fe-Cr-C توسط دانشمند انگلیسی به نام هاری بررلی (Harry Brearley) در 1912 تهیه گردید. اولین ریختهگری تجارتی فولاد ضد زنگ در سال 1913 در شفیلد انگلستان به تولید رسید و حق ثبت آمریکایی جهت این اختراع در سال 1916 به آقای هاری بررلی اهدا گردید.
در دهه 1940، با توسعه تکنولوژی جوشکاری و فرآوری فولاد ضد زنگ، استفاده از این نوع فولاد در صنعت نظامی و صنایع هوا و فضا گسترش یافت. همچنین، در این دوره تلاشهای زیادی برای بهبود مقاومت به خوردگی و زنگ زدگی در محیطهای خاص انجام شد.
در دهههای بعدی، تکنولوژیهای تولید و آلیاژسازی پیشرفت کرده و نوآوریهای جدیدی در زمینه تولید فولاد ضد زنگ انجام شد. با توسعه صنایع خودروسازی، پزشکی، ابزارهای صنعتی و بسیاری از صنایع دیگر، استفاده از فولاد ضد زنگ به شدت گسترش یافت.
در دهههای اخیر، تحقیقات بر روی نانومواد و فناوریهای پیشرفتهتر جهت بهبود ویژگیهای فولاد ضد زنگ انجام میشود. همچنین، تلاشهایی برای افزایش پایداری محیطزیستی و بازیافت مواد نیز در این زمینه انجام میشود.
به این ترتیب، تاریخچه فولاد ضد زنگ از تولید اولین انواع آن تا امروزه پر از انقلابها و پیشرفتهای فنی و علمی است که این نوع فولاد را به یک ماده با ارزش ویژه در جوامع امروزی تبدیل کرده است.
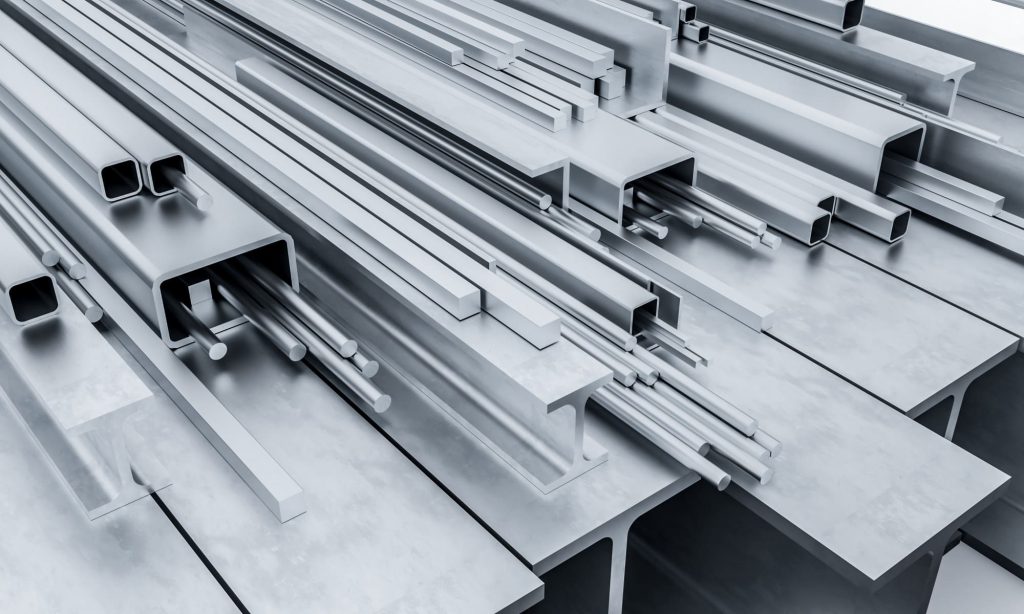
انواع فولاد ضد زنگ
فولادهای ضد زنگ به دلیل ترکیبات خاص خود، مقاومت بالا در برابر زنگ زدگی و خوردگی دارند. این فولادها میتوانند با انواع شرایط محیطی مختلف سازگاری داشته باشند و در بسیاری از صنایع مورد استفاده قرار میگیرند. در زیر تعدادی از انواع معروف فولادهای ضد زنگ آورده شده است:
فولاد ضد زنگ آستنیتیک (Austenitic Stainless Steel):
این نوع فولاد به نام ساختار آستنیتیک خود شناخته میشود که به خاطر دارا بودن کریستالهای کوچکی به نام آستنیت تشکیل میشود. ویژگیهای برجستهای مانند مقاومت به زنگ زدگی، خوردگی، و دارایی در برابر تغییرات دما و خواص مکانیکی مناسب، آن را به یک انتخاب مناسب برای بسیاری از کاربردها تبدیل کرده است.
فولاد آستنیتیک از مقادیر بالایی از کرم و نیکل در ترکیب شیمیایی خود استفاده میکند. این ترکیبات باعث تشکیل لایههایی از اکسید بر روی سطح فولاد میشود که از اکسیژن هوا جلوگیری میکند و از زنگ زدگی و خوردگی محافظت میکند.
فولاد آستنیتیک در بسیاری از صنایع مورد استفاده قرار میگیرد. از جمله کاربردهای آن میتوان به تولید وسایل آشپزخانه، تجهیزات پزشکی، ابزارهای صنعتی، و تجهیزات خودرو اشاره کرد. همچنین، خواص جذاب آستنیتیکها به عنوان مواد ساخت در صنایع هوا و فضا نیز مورد استفاده قرار میگیرد.
سری ۳۰۰ از این نوع فولادها بسیار معروف هستند.
فولاد ضد زنگ فرریتیک (Ferritic Stainless Steel):
این نوع فولاد با تمرکز بر روی ساختار فریتیک خود، که از بلورهای کوبالت متشکل است، شناخته میشود. این فولادها حاوی کروم با درصد بالا و کمی نیکل هستند و با افزودن کروم به فولاد، خصوصیات ضد زنگی این نوع فولاد بهبود مییابد.
فولاد فریتیک به دلیل ساختاری که دارد، دارای خصوصیاتی مانند مقاومت به زنگ زدگی و تغییرات دما میباشد. این نوع فولاد در برخی از محیطها و کاربردها، به دلیل مقاومت خود در برابر خوردگی و استحکام مکانیکی، مورد استفاده قرار میگیرد.
با این وجود، مقاومت فولاد فریتیک به زنگ زدگی و خوردگی نسبت به برخی از دیگر انواع فولاد ضد زنگ کمتر است. به همین دلیل، استفاده از فولاد فریتیک باید با دقت و با توجه به شرایط کاربردی مشخص شود.
از جمله کاربردهای فولاد فریتیک میتوان به برخی از قطعات در صنایع خودروسازی، لوازم خانگی، و تجهیزات صنعتی اشاره کرد. انتخاب این نوع فولاد باید با توجه به خواص مکانیکی و محیطهای استفاده مشخص گردد.
فولاد ضد زنگ مارتنزیتی (Martensitic Stainless Steel):
این نوع فولاد به نام ساختار مارتنزیتیک خود شناخته میشود که به خاطر ریزساختار بلوری خود تشکیل میشود. این نوع فولاد با افزودن کمی کربن به فولاد معمولی تولید میشود و به دلیل ساختار ترکیبی و فرآیند حرارتی خاص، ویژگیهایی منحصر به فرد را به آن میبخشد.
یکی از ویژگیهای مهم فولاد مارتنزیتیک، قابلیت تصلب و سختی بالا است. این خصوصیت باعث میشود که این نوع فولاد در ابزارهای برش، ابزارهای دندانهدار، تیغههای چرخشی و سایر محصولات مشابه مورد استفاده قرار گیرد.
همچنین، فولاد مارتنزیتیک میتواند از طریق فرآیندهای حرارتی مختلف تغییر شکل داده شود. به عنوان مثال، فرآیند تمپر (حرارت دهی مجدد) میتواند خواص مکانیکی این نوع فولاد را تغییر دهد و آن را به منظور تطبیق با نیازهای خاص در انواع مختلف صنایع قابل استفاده کند.
با توجه به خصوصیات فیزیکی و مکانیکی منحصر به فرد، فولاد مارتنزیتیک به عنوان یکی از انتخابهای مهم در صنایع فلزی و مهندسی معرفی میشود که از آن در محصولاتی که به خصوص تصلب و سختی نیاز دارند، استفاده میشود.
آنها دارای مقاومت بسیار بالا در برابر سایش و خوردگی هستند و اغلب در تولید ابزارهای برشی و تیغهها استفاده میشوند.
فولاد ضد زنگ دوفازی (Duplex Stainless Steel):
فولاد دوپلکس یکی از انواع ویژه فولاد ضد زنگ است که از ترکیب ویژهای از دو ساختار فریتیک و آستنیتیک به وجود میآید. این ترکیب باعث ایجاد خصوصیات منحصر به فردی میشود که فولاد دوپلکس را به یک انتخاب مناسب در بسیاری از کاربردها تبدیل کرده است.
از ویژگیهای برجسته فولاد دوپلکس میتوان به مقاومت بسیار بالا در برابر زنگ زدگی و خوردگی، استحکام مکانیکی بالا، و مقاومت در برابر تغییرات دما اشاره کرد. این نوع فولاد به دلیل داشتن ساختار دوفازی، مزایای آستنیتیکها و فریتیکها را ترکیب میکند.
فولاد دوپلکس در بسیاری از صنایع مختلف مورد استفاده قرار میگیرد. از جمله کاربردهای آن میتوان به تجهیزات نفت و گاز، صنایع شیمیایی، تولید ابزارهای صنعتی، و اجزاء در ساخت و تولید خودرو اشاره کرد. همچنین، فولاد دوپلکس به دلیل مقاومت به خوردگی و زنگ زدگی، در محیطهایی که تعامل با مایعات خوردنی یا ترکیبات شیمیایی دارند، به کار میرود.
با توجه به خصوصیات منحصر به فرد و کاربردهای گوناگون، فولاد دوپلکس به عنوان یک انتخاب استراتژیک در صنعت و مهندسی به شمار میآید.
اهمیت مقاومت در برابر زنگ زدگی
مقاومت فولاد ضد زنگ در برابر زنگ زدگی یکی از ویژگیهای بسیار مهم و حیاتی این نوع فولاد است. زنگ زدگی به عملیات اکسیداسیون یا تخریب تدریجی سطح فولاد توسط اکسیژن هوا و ترکیبات شیمیایی موجود در محیطهای مختلف اطلاق میشود. این فرآیند باعث ضعیف شدن و تغییر ویژگیهای مکانیکی و شیمیایی فولاد میشود.
اهمیت مقاومت فولاد ضد زنگ به زنگ زدگی در دستههای مختلف به دلیل موارد زیر بیان میشود:
- حفظ استحکام و ساختار: مقاومت به زنگ زدگی باعث حفظ استحکام و ساختار فولاد میشود. این ویژگی مهم در کاربردهایی که نیاز به استحکام و دوام مکانیکی فولاد دارند، بسیار اهمیت دارد.
- افزایش عمر مفید: فولاد ضد زنگ با مقاومت به زنگ زدگی به طور معمول دارای عمر مفید بیشتری خواهد بود. این امر منجر به کاهش نیاز به تعویض و تعمیرات مکرر شده و همچنین صرفهجویی در هزینههای تعمیر و نگهداری میشود.
- حفظ ظاهر زیبا: مقاومت به زنگ زدگی باعث حفظ ظاهر زیبای فولاد میشود. این ویژگی مهم در کاربردهایی که ظاهر ظریف و تمیزی ضروری است، مانند صنایع آشپزخانهای یا تجهیزات تزئینی، بسیار ارزشمند است.
برای حفظ ویژگی مقاومت به زنگ زدگی در فولاد ضد زنگ، میتوان از روشهای زیر استفاده کرد:
- نظافت و تمیزی منظم: به منظور جلوگیری از تراکم آلودگی و ذرات زاویهدار روی سطح فولاد، نظافت و تمیزی منظم با استفاده از مواد نرم و غیرخشن مهم است.
- جلوگیری از تماس با مواد خورنده: از تماس فولاد با مواد شیمیایی قوی یا مواد خورنده مانند اسیدها و آلکالیها خودداری کنید.
- استفاده از روشهای حرارتی: روشهایی مانند تمپر (حرارت دهی مجدد) میتوانند ویژگیهای مقاومتی فولاد ضد زنگ را افزایش دهند.
- استفاده از روشهای پوششدهی: روشهایی مانند گالوانیزه کردن یا روشهای پوششدهی دیگر میتوانند از سطح فولاد در برابر تماس با مواد خورنده و زنگ زدگی محافظت کنند.
از طریق این روشها و مراقبتهای معقول، میتوان به خوبی ویژگی مقاومت فولاد ضد زنگ در برابر زنگ زدگی را حفظ کرد.
عوامل مؤثر در انتخاب فولاد ضد زنگ
در انتخاب نوع مناسب فولاد ضد زنگ برای هر پروژه، باید به عوامل زیر توجه کرد:
- محیط عملکردی: نوع محیطی که فولاد در آن استفاده میشود، بسیار مهم است. محیطهای خورنده، شیمیایی یا با دماهای خاص نیاز به نوع مناسب فولاد دارند. برای مثال، در محیطهای دریایی با تماس مستقیم با آب شور، فولاد ضد زنگ با مقاومت به خوردگی بالا مورد نیاز است.
- دما و حرارت: میزان دما و تغییرات حرارتی در پروژه بسیار مهم است. برخی انواع فولاد ضد زنگ در دماهای بسیار بالا یا پایین به عملکرد مناسب نمیپردازند. انتخاب نوع مناسب بر اساس دمای محیط و کارکرد طولانی مدت ضروری است.
- خوردگی و تماس با مواد خورنده: اگر پروژه در معرض تماس با مواد شیمیایی خورنده یا تاثیر مواد خورنده قرار دارد، فولاد با مقاومت به خوردگی بالا انتخاب شود.
- ویژگیهای مکانیکی: در پروژههایی که استحکام و مقاومت مکانیکی اهمیت دارد، نوع فولاد با ویژگیهای مکانیکی مناسب انتخاب شود.
- هزینه و بودجه: هزینه تولید و تأمین نوع مشخصی از فولاد نیز میتواند در انتخاب تأثیرگذار باشد. باید تعادلی بین ویژگیهای مورد نیاز و بودجه موجود داشته باشد.
- مقاومت به زنگ زدگی: ویژگی مقاومت به زنگ زدگی در محیط مورد استفاده بسیار مهم است. اگر در معرض تماس با هوا و آب قرار دارد، نوعی فولاد با مقاومت به زنگ زدگی بالا انتخاب شود.
- ظرفیت تولید و پردازش: نوع فولادی که توانایی تولید و پردازش آن در کارخانه موجود را دارید انتخاب کنید.
- بهرهوری و پایداری محیطزیست: در صورت امکان، انتخاب نوع فولادی که به مصرف کمتری از منابع طبیعی نیاز دارد و برای بازیافت مناسب است، توصیه میشود.
از طریق ترکیب همه این عوامل و توجه به نیازهای خاص پروژه، میتوان بهترین نوع فولاد ضد زنگ را انتخاب کرد که باعث بهبود کارایی و دوام پروژه خواهد شد.
کاربردهای فولاد ضد زنگ
فولاد ضد زنگ به دلیل ویژگیهای خاص خود در برابر زنگ زدگی و خوردگی، در بسیاری از صنایع و کاربردها مورد استفاده قرار میگیرد. برخی از کاربردهای اصلی فولاد ضد زنگ عبارتند از:
- صنایع خودروسازی: در تولید قطعات خودرو مانند تعلیق، راهنماها، سیستمهای ترمز و قطعات دیگر از فولاد ضد زنگ بهره برده میشود. این فولاد به دلیل مقاومت به شرایط آب و هوایی مختلف و مواد خورنده موجود در جادهها، بسیار مناسب است.
- صنعت غذایی: در تولید تجهیزات آشپزخانهها از جمله تولید قاشق و چنگال های استیل، تجهیزات نانوایی، تجهیزات پخت و پز و مخازن ذخیره مواد غذایی از فولاد ضد زنگ بهره میبرند. این فولاد به دلیل قابلیت شستشوی آسان و مقاومت به اثرات مواد غذایی مناسب است.
- صنعت پزشکی: در تجهیزات پزشکی مانند ابزارهای جراحی، ابزارهای دندانپزشکی، ایمپلنتها و تجهیزات پزشکی دیگر از فولاد ضد زنگ استفاده میشود. این فولاد به دلیل تحمل به آنتیبیوتیکها و خواص ضد عفونی بسیار مناسب است.
- صنعت نفت و گاز: در تجهیزات نفتی و گازی مانند لولهها، شیرآلات، برجها و تجهیزات حفاری از فولاد ضد زنگ بهره میبرند. این فولاد به دلیل مقاومت به شرایط آبوهوایی تند و تماس با مایعات خورنده در این صنعت اهمیت دارد.
- ساختمانسازی: در ساخت و ساز برخی قطعات مانند میلهها، اتصالات و اجزاء دیگر از فولاد ضد زنگ استفاده میشود. این فولاد به دلیل مقاومت به تغییرات آبوهوا و حفظ ظاهر زیبای خود مورد توجه قرار میگیرد.
- صنایع شیمیایی: در تولید تجهیزات پردازش شیمیایی، مخازن ذخیره مواد شیمیایی و سیستمهای خنککننده از فولاد ضد زنگ بهره میبرند. این فولاد به دلیل مقاومت به تماس با مواد شیمیایی و خوردگی مناسب است.
به علاوه، فولاد ضد زنگ در بسیاری از دیگر صنایع مانند صنایع هوا و فضا، صنایع دریایی، تولید ابزارهای صنعتی و خودروهای لوکس نیز به کار میرود. انتخاب این فولاد به دلیل مزایای طول عمر، دوام، و خصوصیات منحصر به فرد آن در بسیاری از کاربردها بسیار ارزشمند است.
نگهداری و تعمیرات
برای حفظ و نگهداری مناسب از فولاد ضد زنگ و جلوگیری از آسیبهای احتمالی، میتوانید از راهنماییهای زیر استفاده کنید:
- نظافت منظم: سطح فولاد را با استفاده از مواد نرم و غیرخشن تمیز کنید. این کار به جلوگیری از تراکم ذرات و آلودگیها کمک میکند که میتواند به زنگ زدگی منجر شود.
- اجتناب از تماس با مواد خورنده: تماس فولاد با مواد شیمیایی قوی یا مواد خورنده مانند اسیدها و آلکالیها را به حداقل برسانید. در صورت تماس، سطح را به طور دقیق شستشو کنید.
- جلوگیری از تماس با آب پایینکیفیت: آب با مقادیر بالای کلر یا آهن میتواند به زنگ زدگی فولاد منجر شود. از استفاده از آب پاک و پایینکلر استفاده کنید.
- حفظ تهویه مناسب: جلوی تجمع رطوبت در نقاط مختلف بر روی فولاد را بگیرید. تهویه مناسب و جلوگیری از رطوبت میتواند به کاهش زنگ زدگی کمک کند.
- عدم استفاده از مواد خشن بر روی سطح: از مواد خشن و ابزارهایی که میتوانند سطح فولاد را خراشیده یا آسیب برسانند، استفاده نکنید.
- حفظ ظاهر ظریف: از حفظ ظاهر ظریف فولاد اهمیت بدهید. خراشها و ضربات میتوانند به آسیبهای زیبایی و در نتیجه زنگ زدگی منجر شوند.
- محافظت از سطح با روشهای پوششدهی: استفاده از روشهای مانند رنگآمیزی، گالوانیزه کردن یا پوششدهی دیگر میتواند سطح فولاد را از تماس مستقیم با عوامل خورنده محافظت کند.
- استفاده از روشهای حرارتی: استفاده از روشهای حرارتی مانند تمپر (حرارت دهی مجدد) میتواند ویژگیهای مقاومتی فولاد را افزایش داده و از تغییرات نامطلوب جلوگیری کند.
- نگهداری در شرایط مناسب: فولاد را در شرایط مناسب نگهداری کنید. از تماس با شرایط آبوهوایی تند و تغییرات دما به حداقل برسانید.
- نگهداری و تعمیرات منظم: تعمیرات و نگهداری منظم بر روی اجزاء فولادی میتواند از ایجاد مشکلات بزرگتر جلوگیری کند.
با رعایت این راهنماییها، میتوانید از فولاد ضد زنگ بهترین عملکرد و دوام را بدست آورید و از آسیبهای احتمالی جلوگیری کنید.
تفاوت میان فولاد ضد زنگ و ضد زنگنشدنی
تفاوت میان فولاد ضد زنگ و ضد زنگنشدنی در موارد زیر آشکار میشود:
- مقاومت به زنگ زدگی:
- فولاد ضد زنگ (Stainless Steel): این نوع فولاد با افزودن کروم به ترکیب فلزها، مقاومت به زنگ زدگی را تا حد زیادی بهبود میبخشد. کروم به ایجاد پوششی اکسیدی روی سطح فولاد کمک میکند که از تماس اکسیژن هوا و مواد خورنده با سطح فولاد جلوگیری میکند.
- فولاد ضد زنگنشدنی (Non-Stainless Steel): این نوع فولادها به طور معمول دارای مقاومت کمتری به زنگ زدگی هستند و به دلیل عدم حضور کروم یا مواد دیگری که به ایجاد پوشش محافظتی کمک میکنند، ممکن است در معرض خوردگی و زنگ زدگی قرار گیرند.
- ترکیبات شیمیایی:
- فولاد ضد زنگ: این نوع فولادها از ترکیبات شیمیایی خاصی مانند کروم، نیکل و مواد دیگر ساخته میشوند که به افزودن این عناصر متشکل میشوند و ویژگیهای مقاومت به زنگ زدگی را دارند.
- فولاد ضد زنگنشدنی: این نوع فولادها ممکن است از ترکیبات کمتر و متفاوتی تشکیل شده باشند که به طور معمول در مقایسه با فولاد ضد زنگ، مقاومت کمتری به زنگ زدگی دارند.
- کاربردها:
- فولاد ضد زنگ: به دلیل ویژگیهای مقاومتی به زنگ زدگی و خوردگی، در بسیاری از صنایع از جمله خودروسازی، صنعت غذایی، پزشکی و غیره مورد استفاده قرار میگیرد.
- فولاد ضد زنگنشدنی: این نوع فولادها ممکن است در کاربردهایی که مقاومت کمتر به زنگ زدگی میتواند قبول پذیر باشد یا در صنایع مختلفی که نیاز به ویژگیهای خاص دارند، استفاده شوند.
به طور کلی، تفاوت اصلی میان فولاد ضد زنگ و فولاد ضد زنگنشدنی در ویژگیهای مقاومتی به زنگ زدگی و ترکیبات شیمیایی آنها است.